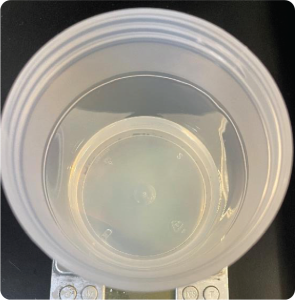
The production of high-quality battery slurries presents many challenges: They are very viscous, contain raw materials that need to be deagglomerated and require highly repeatable/reproducible mixing. Hauschild is therefore presenting its SpeedMixer, which can be used to mix almost any viscosity, at the Battery Show Europe Conference. The power of these centrifugal mixers is so high that particles are reliably deagglomerated and air bubbles and voids are eliminated. Automated programs ensure repeatability.
Hamm/Detroit, xx. October 2021. – The development of high-performance batteries is crucial to enable the effective use of renewable energy sources and to advance the electrification of vehicles, for example. All these developments undoubtedly rely on breakthroughs in materials. Optimizing the anode material is therefore an important area of research, and proper mixing is an essential part of the process.
For batteries, both anode and cathode are usually made by mixing active material (graphite), binder powder, solvents and additives (the keyword is “slurry mix”). This slurry is then pumped into a coating machine, which applies the mixed slurry to the aluminum foil for the cathode and the copper foil for the anode.
Challenge of mixing anodes
Anodes have a variety of compositions for different applications. The most common materials for anodes are carbon/graphite as the active anode powder, carboxymethylcellulose (CMC) as the binder/film former, plus conductive materials and additives, and deionized water as the solvent. Mixing these components then depends on a lot of know-how and experience. Fabio Boccola, CEO of Hauschild Engineering, reveals the procedure required to ensure that the mixing result is convincing. “First, the binder is dispersed in the other powders by dry mixing. CMC tends to clump when added directly to water. Therefore, we recommend using our Hauschild SpeedMixer® to first dry mix the CMC powder with the carbon/graphite powder for about 30 seconds at medium speed. This disperses it and prevents clumping when added to the water. The viscosity/solids content can also be adjusted to the desired values in the final step. In addition, we recommend using a mixing container with a lid that has a small hole in the center to prevent pressure buildup. Mixing under vacuum removes voids/bubbles, dissolved gases and gases adsorbed to fillers/powder.”