Applications
Aerospace and Defense
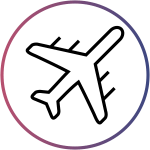
Formulation, preparation, and application of materials for Aerospace and Defense
The Aerospace and Defense markets have some of the highest demands for material performance seen in any industries. There is a constant goal of producing lighter yet stronger parts, all while maintaining the appropriate level of ruggedization to get the job done in even the most extreme environments. This has led to the development and implementation of many advanced materials such as specially formulated epoxies, silicones, urethanes, paints & coatings, ceramics, and even thermal management materials.
Epoxies are frequently used in A&D as adhesives, gap fillers & liquid shims, potting compounds for electronics, impregnated and pre-impregnated (pre-preg) fibers, and even coatings. They are often favored because they are very versatile, easy to work with, and can be processed/cured quickly. They can be formulated with a low viscosity for application like conformal coatings or with higher viscosity and even thixotropic properties when they need to stay in place and not “slump” for applications like abradable materials. Epoxies can be packaged into cartridges or syringes and extruded to simplify handling and application. Their reaction/cure can also often be accelerated with heat to further reduce process times.
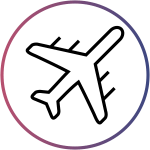
- Epoxy based adhesives are often used in place of or in addition to traditional fasteners. They provide a strong and permanent bond to a variety of materials like metals, ceramics, composites, and foams. They may be mixed with rheology modifiers like fumed silica, flocking for reinforcement, or beads to control the thickness of adhesive between bonded surfaces.
- To achieve the strongest possible bond, surfaces being bonded must be prepared by cleaning & sometimes roughening, epoxy components and additives must be weighed at the correct ratio as specified by the manufacturer, and the system must be mixed thoroughly. A vacuum degassing procedure is also often used to remove bubbles, dissolved gasses, or volatile content that could otherwise create voids or outgas. Once mixed, the epoxy will start to react and must be applied within the “working time” before it begins to gel or harden. The adhesives can often be packaged into cartridges to make application easier and faster so that nearly all the material can be used within the working time and waste is minimized.
- Without epoxy potting compounds many electronics would be much more delicate. These materials are poured over sensitive components and cured in place to ruggedize the system. The cured epoxy creates a hermetic seal which prevents corrosion, insulates electrical components, and makes components more resistant to vibration or shock.
- Potting compounds must be weighed at the correct ratio, thoroughly mixed, and typically vacuum degassed to achieve the best properties. In extreme cases, it may be helpful to apply the epoxy under vacuum. Additionally, or alternatively, potted components can be degassed after epoxy has been applied in order to remove any bubbles/voids formed during the application process.
- Epoxy based materials make effective gap fillers because they can be filled into nearly any size/shape. They can be formulated to be completely flowable so that they can be poured, pumped, or pulled into place with vacuum. In some cases, rheology modifiers like colloidal or fumed silica and reinforcing materials like ground glass or flocking may be added to reduce sag and/or create a more structural material. In cases where weight, machinability, or sandability are more of a concern, hollow glass micro balloons may be added.
- Flowable materials should be mixed thoroughly at the correct ratio to ensure a complete cure and the optimum physical properties. Vacuum degassing may be necessary in some cases, especially if the material will be cured at elevated temperatures or if the material is being pulled into the part with vacuum.
- Rheology modifiers and flocking can often be mixed in at the time of use or predispersed. If modifiers are being used to create a highly viscous system at the point of use, it may be helpful to first mix additives into the resin only so that the hardener can be added after dispersion is complete. This maximizes the working time. Powders and flocking will also introduce air & voids, so vacuum mixing or degassing is also recommended to achieve optimum physical properties. Resin and hardener can be degassed separately or while mixing depending on the amount of degassing that is required and the working time of the material.
- Glass micro balloons are often predispersed and will float to the top/separate with time. If a material containing predispersed glass micro balloons is used, components should either be pre-mixed individually before mixing together, or the entire kit should be used to ensure the correct mix ratio. If glass microballoons are being added to an epoxy at the point of use, it is important to consider that they are most fragile and likely to break when they are dry. They should be mixed in gently, and once fully wetted, a more aggressive mixing cycle may be used. For systems which are highly filled with micro balloons, vacuum mixing can help lower the effective viscosity while mixing due to the gasses expanding and bubbling out of the material. Complete mixing can then be achieved in less time with a less aggressive mixing method which maximizes working time.
- Flowable materials should be mixed thoroughly at the correct ratio to ensure a complete cure and the optimum physical properties. Vacuum degassing may be necessary in some cases, especially if the material will be cured at elevated temperatures or if the material is being pulled into the part with vacuum.
- Epoxy impregnated fiber is the foundation for many of the highest performance aerospace and defense structures in use today. Materials like woven carbon fiber or carbon filaments may be impregnated with epoxy by using vacuum to draw the resin into the fibers or pre-impregnated with epoxy resin for easier handling and layup.
- Using vacuum to impregnate fibers requires that the fibers are laid up dry. The dry assembly is typically placed in an air-tight bag. Vacuum is then used to draw air out of the bag and pre-mixed epoxy resin into the bag, wetting the fibers.
- Pre-impregnated woven fibers or filament can be cut to shape by a robotic cutting table for easy layup or applied directly by a mechanical filament winder. The materials are often kept refrigerated until use to prevent the epoxy from reacting/curing before the material is cut and formed. Once the layup is complete, the part can be cured quickly in an oven.
Regardless of industry, Hauschild SpeedMixer® performs beautifully
Explore our applications
Hauschild Engineering Announces Expanded Support for SpeedMixer
Customers Following Termination with FlackTek Inc.
Let us match you with the Hauschild SpeedMixer® configuration to fit your needs
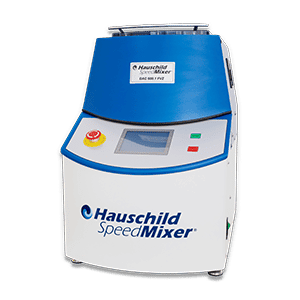
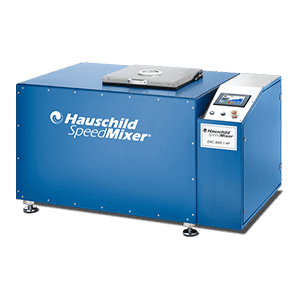
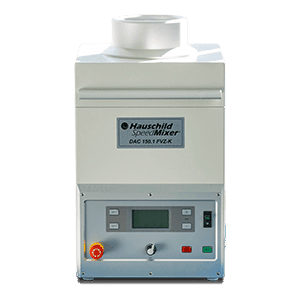
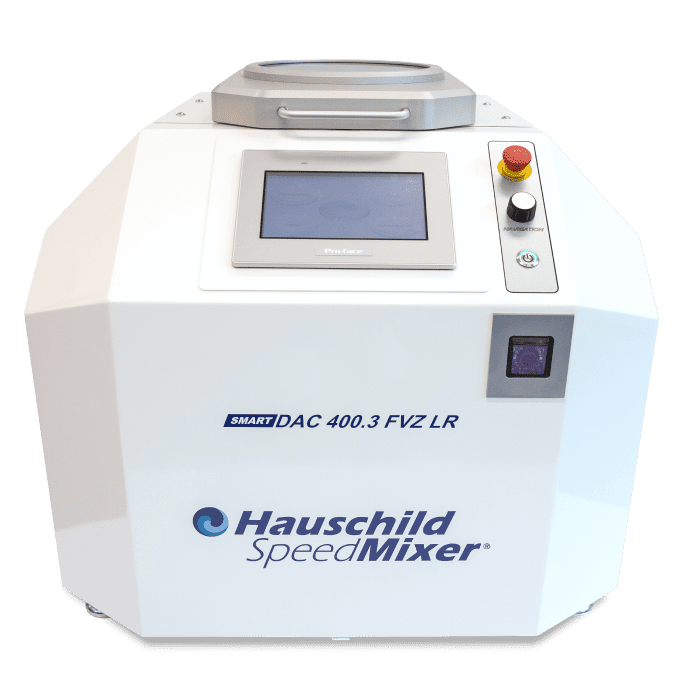
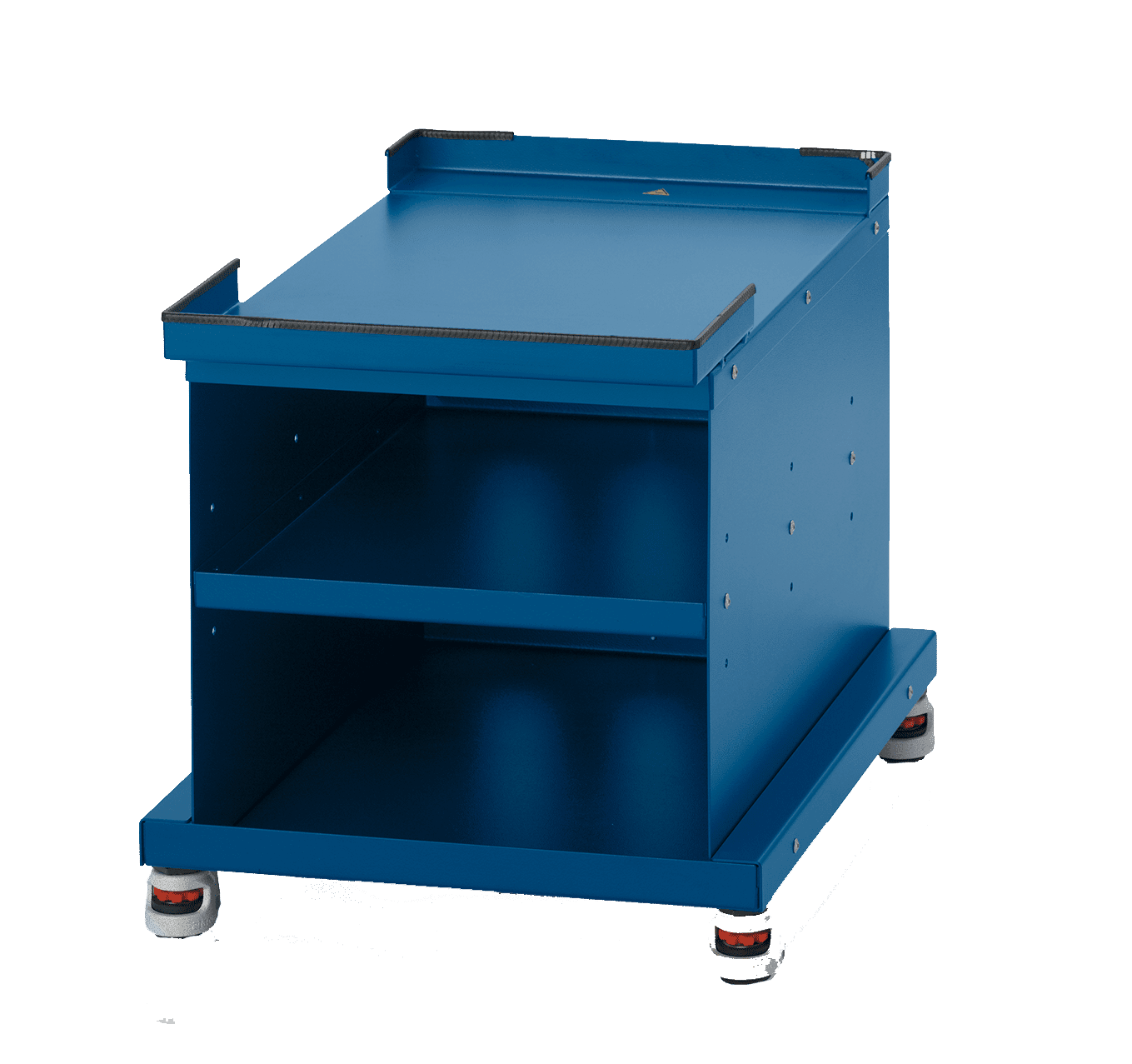